塑胶跑道施工配比的科学调整方法
调整塑胶跑道施工配比需综合考虑材料性能、环境条件、施工工艺及使用场景,以下是关键调整原则及操作指南:
一、核心配比参数调整
甲组分与乙组分配比
基础比例:甲组分(含异氰酸酯≥23%)与乙组分(聚醚多元醇+纳米填料)的重量比为 1:2.5,确保弹性与抗撕裂性(拉伸强度≥0.7MPa)。
黏度控制:混合后黏度需控制在 8000-12000cps,过高或过低均会影响摊铺均匀性。
胶水与颗粒配比
透气型跑道:胶水与EPDM颗粒比例通常为 1:7(胶水占比约12.5%),平衡透水性与防滑性。
混合型跑道:胶水与黑胶粒比例为 1:5(胶水占比16.7%),适用于高强度使用场景。
全塑型跑道:胶水与EPDM颗粒比例为 1:3(胶水占比25%),提升耐磨性和回弹率。
催化剂用量
标准范围:催化剂添加量为总胶量的 0.3%-0.5%,用于调控固化时间(2-4小时)。
高温环境:若温度>30℃,可减少至0.2%-0.3%以延缓反应速度,防止气泡产生。
二、施工环境与配比适配
温度影响
高温(>35℃):减少胶水比例(如透气型调整为1:8),并增加稀释剂(≤胶水量的10%)以降低黏度。
低温(<15℃):提高催化剂用量至0.6%-0.8%,并延长固化时间至6-8小时。
湿度控制
基础含水率需≤5%,湿度>80%时需启动除湿设备,否则胶水粘结力下降30%以上。
气候适应性调整
多雨地区:增加胶水比例至1:4(混合型),增强防水性。
高紫外线区域:添加抗UV剂(占胶水量的1%-2%),延缓材料老化。
三、材料选择与质量控制
颗粒粒径与纯度
底层颗粒:黑胶粒粒径2-4mm,含胶量≥65%,确保弹性层稳定性。
面层颗粒:EPDM彩色颗粒粒径1-3mm,纯度≥95%,避免杂质导致脱粒。
胶水性能验证
环保指标:TVOC≤0.05mg/m³,重金属未检出(符合GB 36246-2024标准)。
粘结力测试:固化后拉拔强度≥0.5MPa(基层与面层间)。
四、配比调整的验证与优化
小样试验
施工前按调整后的配比制作1㎡样品,测试冲击吸收率(≥35%)、垂直变形(≤3mm)等指标。
仪器检测
使用全站仪检测平整度(误差≤3mm/3m),无人机三维建模比对坡度(≤1‰)。
邵氏硬度仪测试面层硬度(60±5),摩擦系数仪检测防滑性(BPN≥60)。
五、常见问题与修正方案
胶水过量导致过硬:减少胶水比例(如从1:5调至1:6),并增加颗粒粒径至3-5mm以提升弹性。
颗粒过多引发脱粒:提高胶水比例至1:4,并减少填料(滑石粉)添加量(≤总颗粒的5%)。
固化不匀或鼓泡:检查催化剂用量是否超标,并确保混合搅拌时间≥5分钟(双轴搅拌机转速35r/min)。
总结
塑胶跑道配比的科学调整需结合材料特性、环境参数、施工工艺三大维度。建议优先选择通过IAAF或GB认证的供应商,并在施工前进行系统性试验验证。若需进一步优化,可参考网页1的工业化标准流程或网页10的混合型跑道配比指南,确保跑道性能与安全双达标。
上一篇:怎样挑选预制型塑胶跑道
下一篇:EPDM颗粒脱落常见的问题
热门更新
推荐阅读
猜你喜欢
关注我们
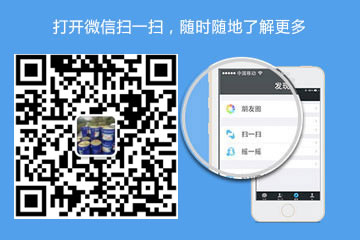